As an engineering student, Laura Vélez knew she wanted to work with utilities, using design to solve environmental challenges. Starting as an intern, and then becoming an associate engineer, for Facilities and Engineering at Amgen Manufacturing Limited (AML), in Juncos, Puerto Rico, she got the opportunity to learn the ins and outs of the highly complex processes used to treat wastewater from biopharmaceutical manufacturing.
“On the manufacturing side, there are all these utilities being used, but they don’t necessarily see all the work that goes on behind the scenes,” Vélez says. “I get to see a lot of what we do and how we distribute water, how we treat it, and all the complications that could have.”
Biopharmaceutical manufacturing relies on a never-ending flow of water to produce a consistent supply of medicines for patients. As sustainability and efficiency become increasingly important today Amgen has also made bold environmental commitments, including setting goals to become carbon neutral by 2027 and to reduce the company’s total water consumption by at least 40%.
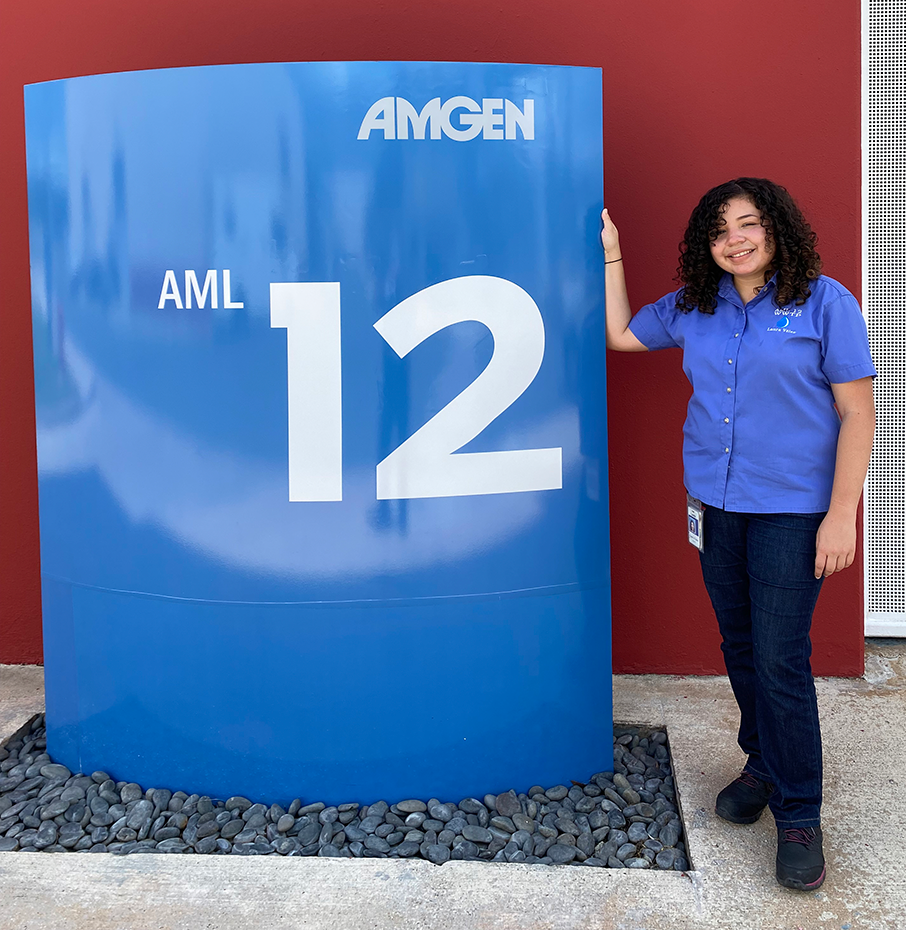
Laura Vélez, associate engineer for Facilities and Engineering, is part of a team of sustainability-focused engineers innovating ways to clean and reuse water at Amgen’s largest manufacturing faciilty.
The Juncos site is Amgen’s largest biomanufacturing facility, which means it’s also the largest user of water, requiring around 450,000 gallons per day for its operations. That demand drove the site to become a hub of innovation where engineers like Vélez work continually to refine the processes for treating large amounts of wastewater, while also engineering new ways to reuse and significantly improve the overall efficiency of the site’s water use.
The path to becoming a leader in wastewater treatment for biotech
“Amgen’s Puerto Rico manufacturing facility had no on-site wastewater treatment capabilities 16 years ago,” explains José Martínez, senior manager of Environmental Health, Safety & Sustainability at Amgen’s Juncos facility. “Municipal water was taken in each day, and after one use, it was pumped into a fleet of 15 tanker trucks to be transported to local government facilities for treatment.”
As products and regulations changed, it became clear that the facility needed a way to treat wastewater on-site. “When it was decided to build a wastewater treatment plant, we said it needed to be a state-of-the-art system to ensure that it would continue serving our needs long into the future,” Martínez adds.
Today, this area of operations is not only focused on treating wastewater from biomanufacturing processes, but also on recapturing and reusing water from throughout the facility, to reduce usage everywhere, from the bioreactors to the restrooms and the outdoor landscaping.
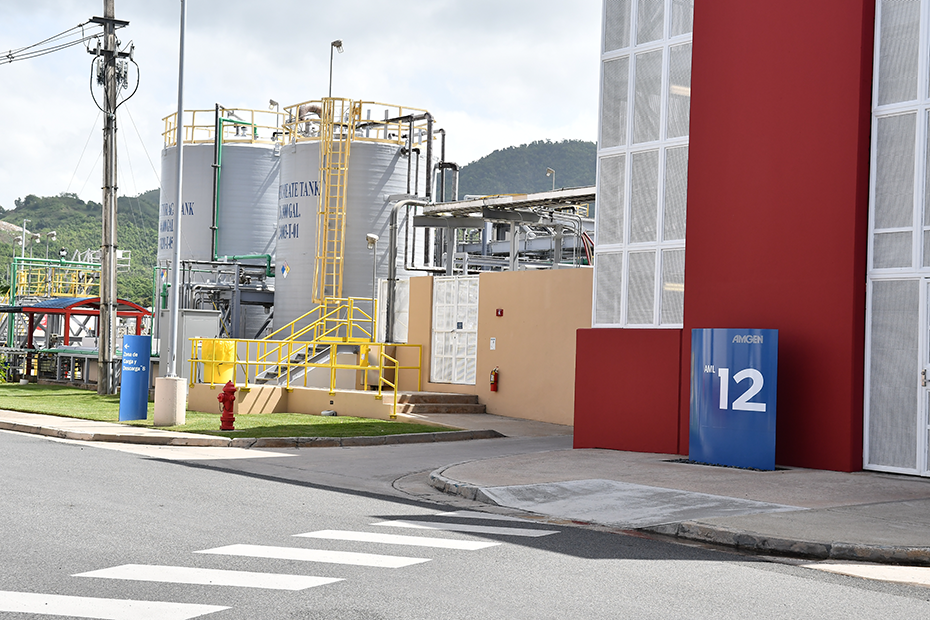
The wastewater treatment plant occupies building 12 at Amgen’s sprawling manufacturing facility in Juncos, Puerto Rico, helping ensure more sustainable operations and continuous supply of medicines for patients.
“On the wastewater side, the biggest challenge is that we’re maintaining a living system, called an activated sludge system,” Vélez says. “It’s a huge colony of bacteria that treats the water, so we need to feed it well, and make sure it stays at the right temperature, and has the right amount of oxygen to breathe—it's almost like taking care of a child.”
This activated sludge process has become standard for wastewater treatment today. Still, one unique aspect of Amgen's Puerto Rico system is how the water gets filtered. “We use a more expensive and more advanced technology called membrane bioreactors,” Vélez says. “Most wastewater treatment plants just use simple settling tanks, which require a lot of space and time but cost less to operate. By filtering through a membrane, we can clean the same amount of water faster, and with a much smaller footprint.”
The entire site in Puerto Rico is designed to use as much as 500,000 gallons per day, but it currently uses around 450,000 gallons per day. “Of that total water, 25% ends up as a waste brine that must be cleaned and sent to the sewer, so a little more than 100,000 gallons goes to the sewer as clean water, which means we're not introducing additional waste into the island’s water treatment system,” says Juan Javier Díaz Cosme, senior manager, Maintenance, for the wastewater treatment plant in Puerto Rico. “The remaining water, approximately 337,000 gallons per day, is reusable. The result is nearly 250,000 gallons of water daily that we’re no longer buying or bringing from outside.”
A long history of compliance and recognition for sustainability efforts
For companies like Amgen, the operation of manufacturing facilities comes with regulatory oversight from U.S. government and local Puerto Rican environmental protection agencies. These important agencies monitor things like waste and emissions coming from manufacturing facilities. Since it was first created 15 years ago, the wastewater treatment plant at the Juncos facility has maintained a perfect record of compliance.
“We've never had a notice of violation, and we’re committed to operating wastewater treatment in compliance with regulations,” says Judith Velázquez, executive director of Engineering Services for Amgen in Puerto Rico. “We have a responsibility as Amgen to operate according to our values.”
Recently, Vélez attended a sustainability summit held by the Puerto Rico Manufacturers Association as a representative for her Facilities and Engineering function. At the event, Amgen was awarded gold-level recognition for its sustainability efforts in the categories of water conservation and sanitary waste. “Water conservation is one of the hardest things to do when your product is mostly made with water,” Vélez says. “Being there to represent Amgen was one of my biggest highlights.”
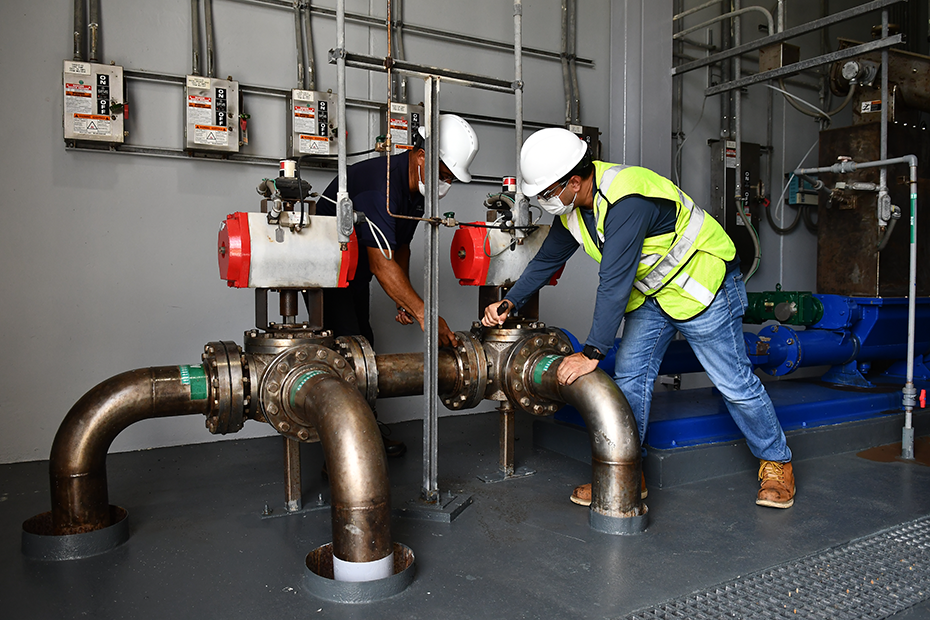
Workers at Amgen's Juncos facility perform system maintenance on the wastewater treatment plant.
Looking to an even more sustainable future
Amgen’s wastewater team in Puerto Rico has kept their facility on the cutting edge, but they aren’t resting on their laurels. Their ambitious goals for the future are to continue finding new ways to reuse water and driving toward an even more efficient system.
“We currently reuse around 50-60% of our water—compared to other companies, that’s a lot,” Martínez says. “At today’s level of sophistication there will always be some amount of water that can’t be reused after treatment, but we’re continuing to look for ways to close that gap and reuse as much as possible, including in places like utilities, cleaning the buildings’ roofs and outdoor areas, and in landscaping and firefighting activities.”
They’re also looking for other ways to reduce waste, such as converting the solid byproducts from wastewater treatment into nutrient-rich compost.
“Designing water systems with sustainability in mind is something we're going to have to work on continually,” Vélez says. “Doing this work creates value for the company, of course, but it’s about more than just us—it’s also about improving the world we live in. We don't have the same resources that we had 50 years ago. That's why I'm really passionate about water.”